Tungsten carbide stamping dies are indispensable tools in modern manufacturing, revered for their exceptional hardness, wear resistance, and ability to produce high-precision components with remarkable consistency. As industries increasingly demand tighter tolerances, extended tool life, and higher production volumes, the role of tungsten carbide in stamping operations has become more critical than ever. This article delves into the material science, design considerations, manufacturing processes, and applications of tungsten carbide stamping dies, highlighting their pivotal contribution to advanced industrial production.
The Unrivaled Material: Tungsten Carbide (WC-Co)
At the heart of a tungsten carbide stamping die lies its namesake material: a composite primarily consisting of tungsten carbide (WC) particles embedded in a metallic binder, most commonly cobalt (Co).
- Tungsten Carbide (WC): This ceramic phase is incredibly hard, possessing a Vickers hardness often exceeding 1600 HV, significantly higher than hardened tool steels. This intrinsic hardness is responsible for the die's resistance to abrasive wear, plastic deformation, and indentation.
- Cobalt (Co) Binder: The cobalt binder acts as a cementing agent, holding the hard WC particles together. While cobalt itself is softer, its ductility and toughness impart crucial properties to the composite, preventing catastrophic brittle fracture of the WC grains. The percentage of cobalt (typically ranging from 3% to 25% by weight) significantly influences the final properties of the carbide. Lower cobalt content leads to higher hardness and wear resistance but reduced toughness, making it suitable for applications requiring extreme wear resistance. Conversely, higher cobalt content offers increased toughness and impact resistance at the expense of some hardness, ideal for operations involving shock loads.
- Microstructure: The performance of tungsten carbide is also heavily dependent on its microstructure, specifically the WC grain size. Fine-grained carbides (sub-micron to 1 micron) offer superior hardness and edge retention, making them ideal for precision stamping of thin materials. Coarse-grained carbides (above 5 microns) generally exhibit higher toughness and are preferred for heavier blanking or forming operations.
Advantages of Tungsten Carbide Stamping Dies
The superior properties of tungsten carbide translate into a multitude of benefits for stamping operations:
- Exceptional Wear Resistance: This is the primary advantage. Tungsten carbide dies can withstand millions, and in some cases, tens of millions of strokes before significant wear occurs, drastically reducing downtime for tool changes and maintenance.
- High Hardness: Their extreme hardness allows them to cleanly cut and form a wide range of materials, including high-strength steels, stainless steels, electrical steels, and non-ferrous alloys, with minimal deformation of the die itself.
- Dimensional Stability: Tungsten carbide exhibits excellent resistance to plastic deformation under high compressive loads, ensuring the stamped parts maintain consistent dimensions and tight tolerances throughout the production run.
- Superior Surface Finish: The inherent hardness and fine grain structure of tungsten carbide allow for highly polished working surfaces, which minimizes friction during stamping and contributes to a better surface finish on the stamped components.
- Reduced Galling and Adhesion: Compared to steel dies, tungsten carbide has a lower tendency to gall or experience material adhesion, particularly when stamping sticky or abrasive materials.
- Longer Tool Life: The cumulative effect of these advantages is a significantly extended tool life, leading to lower per-part costs, increased productivity, and a more stable manufacturing process.
Design Considerations for Tungsten Carbide Stamping Dies
Designing with tungsten carbide requires a specialized approach, acknowledging its inherent brittleness compared to tool steels while leveraging its extreme hardness.
- Minimizing Stress Concentrations: Sharp corners, abrupt changes in cross-section, and re-entrant angles must be avoided as they create stress concentration points where cracks can initiate. Generous radii and gradual transitions are crucial.
- Support and Compressive Loading: Tungsten carbide performs best under compressive loading. Dies must be designed with robust backing plates and inserts that provide full support, preventing tensile stresses or bending moments on the carbide components. Shrink fitting carbide inserts into steel holders is a common practice to pre-stress the carbide in compression.
- Material Thickness and Clearance: The thickness of the material being stamped and the required cutting clearance are critical factors in selecting the appropriate carbide grade and designing the die geometry. Thicker materials or higher blanking forces generally require tougher carbide grades.
- Lubrication and Cooling: Proper lubrication is essential to minimize friction, dissipate heat, and extend die life. The die design should accommodate effective lubrication delivery and coolant flow.
- Modularity and Replaceable Inserts: Due to the cost and manufacturing complexity of large carbide blocks, dies are often designed with modular carbide inserts that can be individually replaced when worn, rather than replacing the entire die assembly.
- Grinding and EDM Allowances: As tungsten carbide is extremely hard, it can only be machined by specialized processes like grinding (using diamond wheels) or Electrical Discharge Machining (EDM). The design must account for these manufacturing limitations and provide sufficient material for post-sintering finishing operations.
Manufacturing Processes
The production of tungsten carbide stamping dies involves several specialized steps:
- Powder Metallurgy: The process begins with precise blending of WC and Co powders, along with other minor additives (e.g., grain growth inhibitors).
- Pressing: The mixed powders are then compacted into a "green" (un-sintered) shape using mechanical or isostatic presses. The pressing method influences the density and homogeneity of the green compact.
- Sintering: This is the critical step where the green compact is heated in a vacuum furnace to temperatures close to the melting point of the cobalt binder (typically 1300-1500°C). During sintering, the cobalt melts and wets the WC particles, leading to densification and the formation of a strong, coherent structure. Some porosity may remain, and further densification can be achieved through Hot Isostatic Pressing (HIP).
- Grinding and Finishing: After sintering, the carbide parts are extremely hard and require diamond grinding wheels for precision shaping and achieving the final dimensions and surface finish. Complex geometries may also utilize Wire EDM (Electrical Discharge Machining) or Ram EDM for intricate features.
- Coating (Optional): For highly demanding applications, a thin, super-hard coating (e.g., TiN, TiCN, AlTiN, CrN) can be applied via PVD (Physical Vapor Deposition) or CVD (Chemical Vapor Deposition). These coatings further reduce friction, improve wear resistance, and extend tool life, especially when stamping abrasive materials or those prone to galling.
Applications of Tungsten Carbide Stamping Dies
Tungsten carbide stamping dies are critical in industries where high precision, long tool life, and high-volume production are paramount. Common applications include:
- Electronics Industry: Stamping of lead frames, connectors, terminals, heat sinks, and other miniature components for consumer electronics, automotive electronics, and telecommunications.
- Automotive Industry: Production of electrical contacts, precision shims, small mechanical components, and components for ABS systems and fuel injection systems.
- Medical Device Industry: Manufacturing of precision components for surgical instruments, implantable devices, and diagnostic equipment, where extremely tight tolerances and biocompatibility (in some cases) are essential.
- Aerospace Industry: Stamping of lightweight, high-strength alloy components for aircraft and spacecraft, demanding exceptional reliability and performance.
- Appliance Industry: Production of various small, intricate parts for household appliances.
- Watchmaking and Jewelry: For intricate and precise stamping of small, decorative, and functional components.
Challenges and Future Trends
Despite their significant advantages, tungsten carbide dies present certain challenges:
- Cost: The raw materials and manufacturing processes for tungsten carbide are significantly more expensive than those for tool steels.
- Brittleness: While tough for a ceramic, tungsten carbide is still more brittle than steel, making it susceptible to chipping or catastrophic failure under extreme shock loads or improper handling.
- Machinability: Their extreme hardness makes them difficult to machine, requiring specialized and often slower processes like diamond grinding and EDM.
Future trends in tungsten carbide stamping die technology are focused on:
- Advanced Grades: Development of new carbide grades with improved toughness-to-hardness ratios, finer grain structures, and enhanced resistance to specific wear mechanisms.
- Improved Coatings: Research into more durable, lower-friction, and application-specific coatings that can further extend tool life and optimize performance.
- Additive Manufacturing: While still in its early stages for functional carbide dies, additive manufacturing (e.g., binder jetting with subsequent sintering) holds promise for creating complex geometries and internal cooling channels that are difficult to achieve with conventional methods.
- Predictive Modeling: Increased use of finite element analysis (FEA) and other simulation tools to optimize die design, predict performance, and identify potential failure points before manufacturing.
Conclusion
Tungsten carbide stamping dies represent a pinnacle of material science and engineering in precision manufacturing. Their unparalleled hardness and wear resistance enable industries to achieve higher levels of precision, productivity, and cost-effectiveness. As manufacturing demands continue to evolve, the ongoing innovation in tungsten carbide materials, design methodologies, and processing technologies will ensure that these extraordinary tools remain at the forefront of high-performance stamping operations for the foreseeable future.
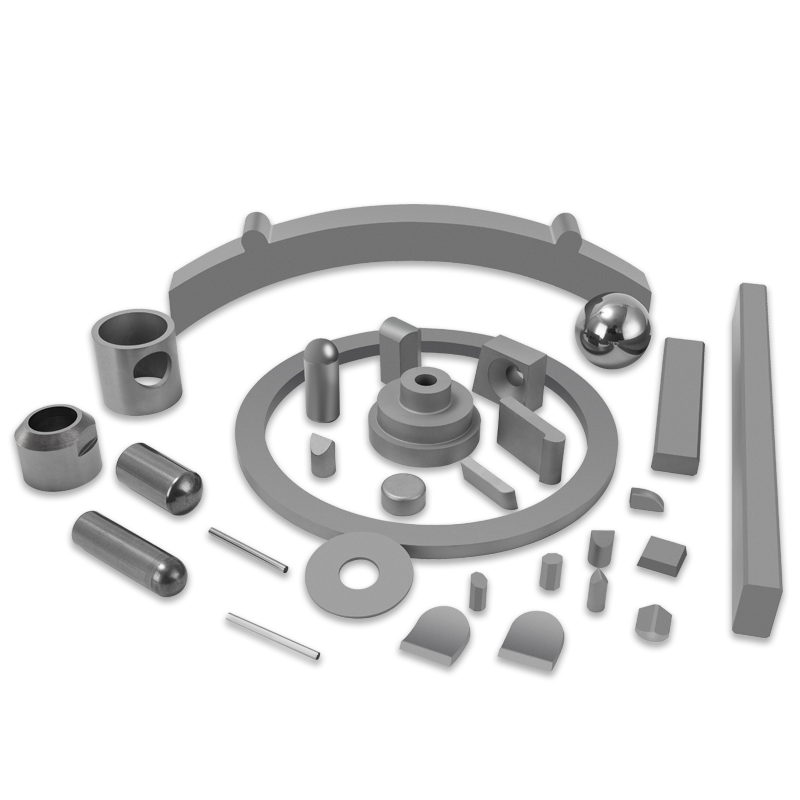